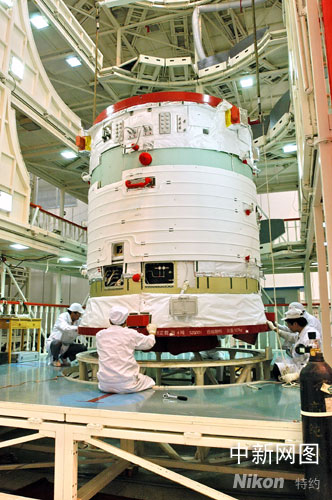
中国神舟七号载人航天飞船发射在即。飞船推进舱起吊(资料图片)。
|
中国神舟七号载人航天飞船发射在即。飞船推进舱起吊(资料图片)。
|
中新网9月26日电 题:神舟七号飞船研制纪实之推进舱:全面改进 便于“出舱”
作者:游本凤
众所周知,神舟七号飞船飞行任务由于将实施航天员出舱这一重大创新活动,以及乘坐3位航天员,飞船总体技术状态出现较大变化。而对于承担了神舟七号飞船上推进舱、电源分系统、推进分系统和遥控通信9个子系统等重要研制任务的中国航天科技集团上海航天技术研究院来说,技术状态也要随着任务的变化和总体的变更而变,随着飞行任务的不同要求和目标而变,这就需要他们以变应变,不断用技术创新和更严格的质量来满足“神七”飞行任务的要求。
与神舟六号飞行状态相比,神舟七号技术状态更改共200多项,而涉及到该院承制任务变化的有43项,其中一类更改6项,二类更改37项。涉及产品有推进舱、舱内和舱外摄像机、电源分系统、总体电路等。有些由于总体技术状态和涉及到有关出舱产品一直处于变动之中,留给他们的时间非常紧张。如由该院承担研制的推进舱在技术状态上的变化较大,考虑到这次出舱活动,相应的设备要增加十多台。而增加的设备大小不一、轻重不一,功能作用不一,因此不能简单地往推进舱里一安装就了事。毕竟一下子多了十多台设备,推进舱总体单位在设计时既要充分考虑到舱体在太空飞行过程中的重心和平衡,还要根据产品体积的大小安装在合适的位置,再就是要考虑安装时操作人员的操作和检修时的方便,等等。各种因素很多,必须综合权衡,使得设计方案科学合理,安装调试一步到位。
由于都是第一次碰到出舱活动带来的技术状态变化,总体单位和有些设备研制单位在设备技术指标和其他方面一直在变化。这使得推进舱研制周期成为历次研制中时间最长的一次,如果再拖延的话,将要影响到整船对接的联试和模飞。2006年8月11日,工程总体一位领导到该院检查指导“神七”研制工作时,听到对此事的汇报后指示,“神七”是国家任务,是2008年我国的大事之一,举世关注,研制时间只能往前赶,不能拖延。院里当即立下了军令状,要求主要研制单位上海航天设备制造总厂必须确保产品于9月10日出厂。
只有一个月的时间,却要完成平时需要几个月才能完成的任务。这对上海航天设备制造总厂来说压力太大了。破釜沉舟,没有退路,该厂厂长也下了死命令:后墙不倒,就是天天加班连轴转也要赶出进度来!正是在这样的“高压”之下,该厂飞船线上的同志克服一切困难,连续数周每天工作12小时以上,可谓开足了马力。经过上下艰苦努力,终于实现诺言,推进舱按期出厂。
电子所针对这次新增气闸舱和航天员出舱活动,增加了舱外摄像机等与“神舟六号”技术状态完全不同的七台新设备。这些设备主要目的是加强地面控制中心与空间航天员图像与信息的传输,实现航天员与地面的双向通话。尤其是舱外摄像机将锁定航天员出舱,保证航天员在舱外的一举一动受控,确保航天员的生命安全。还有飞船返回着陆后,由新设备发出定位信标信号,以便地面搜索人员尽快寻到航天员。这对于电子所来说,既是机遇,也是压力。电子所的科技人员顾全大局,以“神七”任务为重,迎难而上,奋力攻关,克服了难以想象的困难,最终通过苦干加巧干,在预定计划时间内完成了交付任务。
上海航天技术研究院在“神七”研制过程中,适逢院部和部分研制单位进行调改整合,以及搬迁航天新区,如将三家单位整合为一家后一同搬迁新区。融合后的三家单位碰到了机制体制、观念文化等方面的一系列矛盾,而其中的一个所又是“神七”上控制通信设备研制关键单位。面对矛盾,要紧的是统一思想,理清思路,将所有的工作按轻重缓急弹好“钢琴”。其间,型号“两总”多次深入到该所科研生产一线进行指导,当场拍板帮助解决实际问题,调动了一线科技人员的积极性,使得研制进度大大加快。正是在大家的共同努力下,该院做到了搬迁新区和科研生产两不误,两促进。另外,在调改过程中,院里还决定将其中一个所承担研制飞船电源分系统中的一块兼并到另一个空间电源专业所,进行专业重组。这也是上海航天技术研究院在“神七”研制关键时刻采取的一项重要举措。尽管在调改兼并过程中也同样碰到了不少矛盾和阻力,但最终大家还是达成共识,认为这一举措有利于电源专业的发展和壮大,有利于专业的对口管理,也有利于提高核心竞争力。个人的事再大也小,飞船的事再小也大。于是,原先单位兼并过去的同志很快调整好情绪,转换好角色,服从大局需要,全力以赴地投入到“神七”研制中。
狠抓质量 力保飞天平安
作为航天行业,质量历来被放在至高无上的地位。而对于载人航天来说,质量更是关系到航天员的生命安危。没有质量,就没有航天员生命安全的保证。因为飞船上有了人,对航天产品质量的要求和标准必须严之又严,高之又高,决不能有半点闪失。
上海航天技术研究院从“神舟一号”起,在整个飞船线上就牢牢树立了严慎细实的质量理念和意识,坚持贯彻“步步为营、节节把关;上挂下连、吃透技术;前延后伸、跟踪质量”十六字全过程质量控制措施,策划全过程质量管理活动。同时针对该院承担任务的特点,制定了“神舟七号”质量控制要点。严上加严,细上加细。在具体操作上,该院针对以往发生质量问题后,要求各单位进行兜底翻、查源头,还专门制作了神舟飞船产品质量数据包。数据包是设计输入、技术状态控制、可靠性安全性分析、工艺、物资、测试试验、关重项目控制等84份文档资料的总称。数据包工作能有效地将单机的质量控制关口前移,注重单机形成的每个环节的质量控制,使得单机在交付后对其履历的每个阶段都能做到有据可查,有源可寻。飞船副总指挥兼副总设计师秦文波对数据包的建立非常重视,曾多次在有关大会和小会上呼吁,强调其重要性和科学性。从实际工作效果来看,“神七”质量管理数据包确实起到了很重要的作用,尤其在整个“神七”研制过程中,对所出现的问题,至少在寻根溯源上用很短的时间就可以找到。
在“神七”研制中,科技人员深深感到,质量工作千头万绪,稍有不慎,就会出错。既要靠各项制度来保证,又必须要靠提升责任心来加强。精心实施,精心操作,不留隐患,从各个方面提高飞船的质量和可靠性,确保万无一失。上海航天设备制造总厂在推进舱总装过程中,事先制定了总装质量控制要求和详细的质量工作计划。总装工人实施班前工作会制度,使每一个工人在上班前就明确每天的工作内容、操作注意事项和质量要求。该厂还成立了现场服务小组,对生产过程进行监督和控制。尤其对关键点,即总装过程中的电连接器插拔情况进行了详细记录,特别对关键接口随时进行检查。正因为严格把关,杜绝了推进舱在总装过程中的差错,至总装调试结束,推进舱未发生一例电连接器错插或漏插的情况,确保了总装过程准确无误,无一差错。
驱动机构是飞船上电源分系统太阳电池翼展开的关键件,为了确保其在太空中准确无误地打开,研制人员作了大量有针对性的试验,如根据电源系统对神舟七号飞船电源分系统供电能力分析结果,电源分系统驱动机构在轨工作时,通过驱动机构的最大充电电流为29A。由于“神舟七号”电源分系统驱动机构在地面只进行了额定23A电流的试验,为验证在轨运行期间驱动机构通过最大充电电流29A的能力,需在地面进行补充验证试验。接到任务后,设计人员立即制定了详细的任务书,根据具体的步骤,在热循环箱中进行了充分试验,最后驱动机构经过5个循环的模拟在轨运行加电试验后,电压降等技术指标满足要求,焊接工艺的稳定性也得到了考核,保证了充电电流的全覆盖性,确保了“神舟七号”驱动机构不带一点疑问上天。同样,活动机构一直是航天器产品中的薄弱环节,技术难度大,但是对产品的可靠性要求非常高,关系到整个飞行试验的成败。为了保证“神舟七号”太阳电池翼能够可靠展开,单位组织专业人员对神舟七号太阳电池翼的展开过程进行了动力学仿真复核复算,一是保证能够顺利展开,二是尽量减少电池翼展开时对飞船的撞击力,从而达到对飞船姿态影响最小的目的。这一措施也取得了较好的效果。
上海航天设备制造总厂在“神七”研制中,对导线的端头处理采用了热剥的工艺方法,代替原来属航天限用工艺的冷剥工艺方法。神舟飞船的导线的屏蔽层耐高温性好,热剥操作非常困难,传统的热剥工具无法满足要求。为解决这一难题,电装工艺人员多方调研,并进行了大量的工艺试验。最终,选定了合适的热剥工具和工艺参数。经试验,新热剥工具能够满足“神七”热剥的要求,并通过了院级评审。热剥工艺的应用,提高了工效和质量可靠性,确保了“神七”飞行任务的万无一失。
![]() |
更多>> |
|